APM Terminals’ new shipping line dashboard reduces port stay
Already live at four APM Terminals locations (Onne, and Apapa, Nigeria; Algeciras, Spain; and Progreso, Mexico), it will be able to roll the Dashboard out to 7 more terminals by the end of this year.
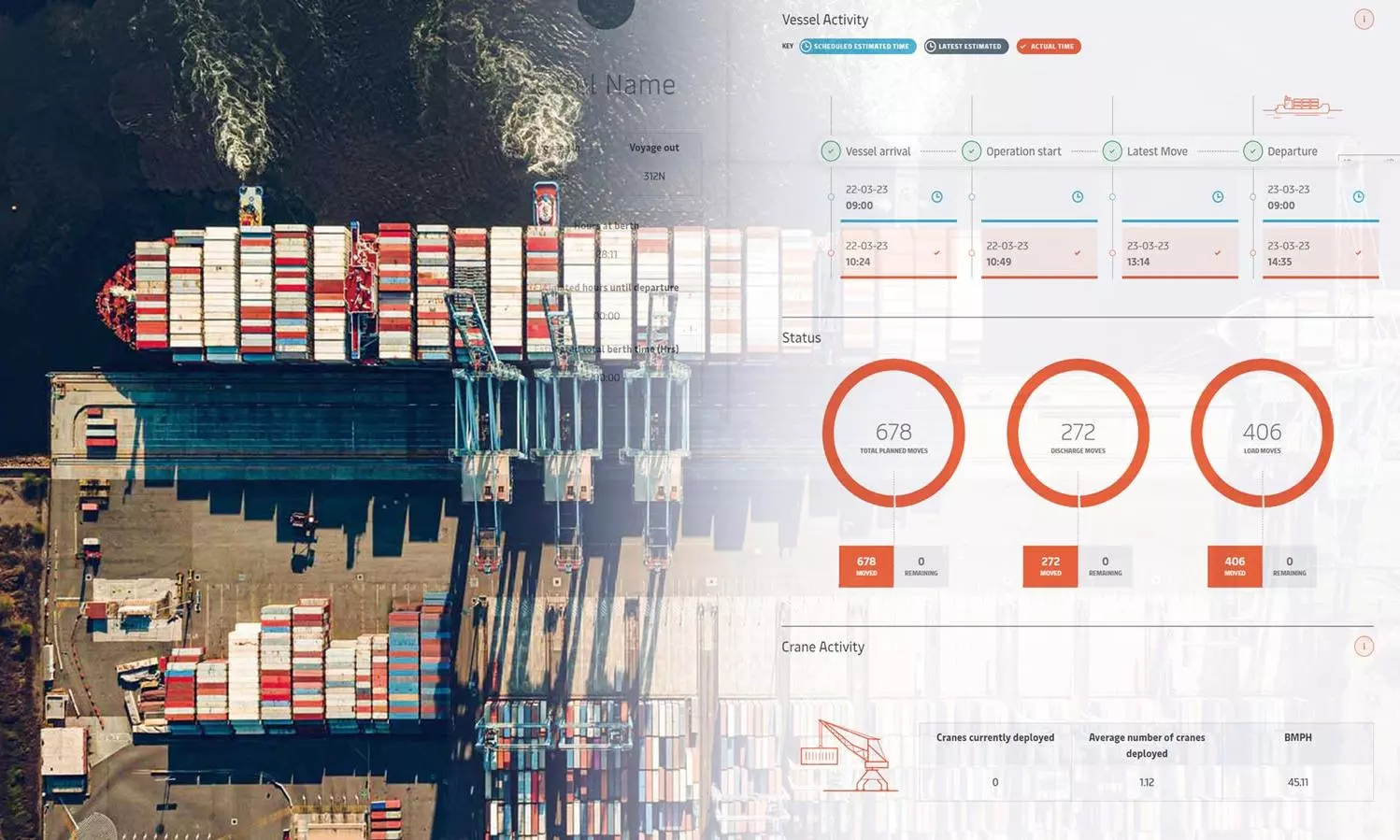
With stormy seas forecast for shipping lines next year and decarbonisation high on the agenda, the pressure on container terminal operations to reduce port stays has never been more urgent.
“The biggest gains will come from companies who improve cooperation between shipping lines and terminals,” says Laura Bercan, responsible for Visibility Products at APM Terminals. APM Terminals newest visibility solution, the Shipping Line Dashboard, will provide the foundation to open this dialogue, she says.
Reducing port stays is a key focus for APM Terminals. In addition to ongoing investment in port equipment and the implementation of lean methodologies to lift standards of efficiency, much of the low hanging fruit has already been picked. APM Terminals has already identified 100s of process improvements to shave off precious minutes in port.
“Pre-rigging the safety net for the gangway saves around 10-15 minutes,” says Laura. “We're able to reduce delays on tugs or pilots arriving on time through improved processes; and prepare crane deployment even before the gangway is down. I could name many more examples, but the biggest wins are still to be had.”
Reducing port stays will however take even greater collaboration. Improved stowage plans to reduce moves, increased dual cycles and tandem lifts and optimised crane splits to ensure all cranes complete at the same time, will all contribute to achieving the biggest improvements, at little extra cost.
“The improved visibility and predictability offered by our new Shipping Line Dashboard can provide a great starting point for these conversations,” says Laura. “Furthermore, the solution is built in accordance with the DCSA's Interface Standard for Just-in-Time Port calls. This enables operational port-call data from the Dashboard to be digitally shared with other industry parties in a consistent manner. This can help synchronise upstream vessel-port activities and improve efficiency.”
The Shipping Line Dashboard provides shipping operators with real-time, 24/7 self-service online access to current vessel schedules and the operational status of a vessel at berth. This includes completed moves and outstanding moves (loading and discharging), reliable estimated times until completion and efficiency statistics for each crane working on the vessel.
Ultimately the Dashboard can help shipping lines better estimate bunkering requirements and onward planning. It removes the need to call the terminal, provides 24/7 transparency, removes human bias and error in estimates, and makes guesswork a thing of the past.
Already live at four APM Terminals locations (Onne, and Apapa, Nigeria; Algeciras, Spain; and Progreso, Mexico), the company’s global approach to developing digital solutions means that it will be able to roll the Dashboard out to 7 more terminals by the end of this year.
“The delivery of the Shipping Line Dashboard marks an important step in our digital transformation and product development focused on shipping operators,” says Laura.
She adds that there is much more still to come: “We expect this product to evolve with our customers’ needs, and that will get us even closer to being the World’s Best Terminal Operator.”